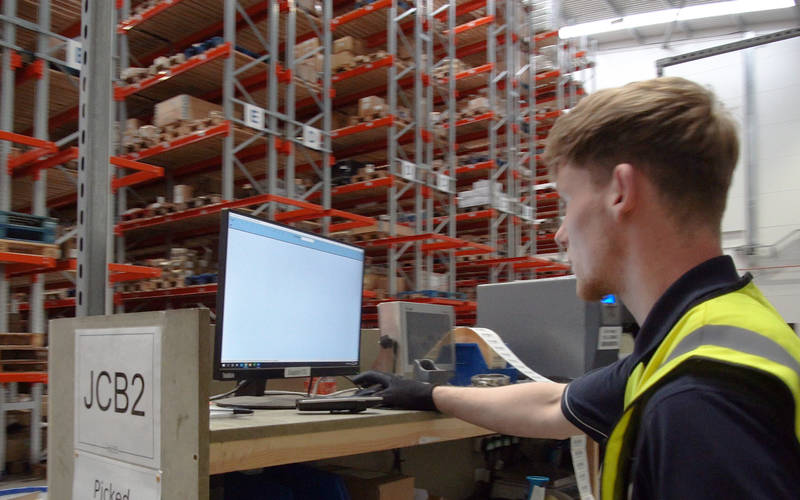
Mitigating Supply Chain Disruptions in the Global Industrial Arena
By James Smetham, Managing Director – Europe and Asia, Supply Technologies
The world is experiencing unprecedented levels of disruption. Conflicts, raw material shortages, pandemics, protectionism, and labour shortages are all contributing towards making global supply chains more complex than they were ever anticipated.
All these factors are not only causing friction on supply chains, but also creating a formula for inflation. Volatile supply chains result in unplanned premium expenditures, inefficient factory production productivity, and lumpy working capital that strains cash flows.
Supply Technologies specialises in managing complex supply chains for an array of different market sectors. With a team of over 1,000 supply chain experts across the globe, Supply Technologies helps its customers build products better, smarter, and faster.
Based on our extensive experience, here are a few focus areas that can be utilised to mitigate the impact of supply chain disruptions and stabilise the resulting impacts:
Demand Management & Communication
With the restrictions of the COVID-19 pandemic, consumers have developed a pent-up appetite for goods and services. Businesses reduced capacity during the pandemic, and this, combined with a recovering but fractured global logistics trade network, has resulted in extended lead times and a lack of supply.
In attempting to meet strong demand, B2C businesses have developed ambitious factory build rate plans often in excess of their factories’ supply chain capabilities. Rather than moderate plans reflective of both the factories’ capacity and supply chain capabilities, many B2C businesses have retained their build rate plans on the basis that if they can get the materials and labour, they can produce and meet demand.
When output does not meet the build plans, supply chain partner trust reduces, inventory gets built up in various stages of the supply chain, and lumpy demand ensues causing the start the bullwhip effect.
Now, more than ever, it is imperative that businesses carefully assess the capabilities of both their production capacity and their supply chains to create pragmatic production plans that can be accomplished, maintained, and bring stability to the supply chain reducing the demand variability of the bullwhip effect.
Regular Sales and Operation Planning (S&OP) sessions are a great way for organisations to establish and clearly communicate the varying dynamics of customer demand fluctuations, factory capacity, through to supply chain constraints level loading demand to capabilities.
Deploying enhanced Supply Chain Visibility tools, where communication can be enhanced to enable a high degree of demand information to flow up and down the chain, can regain supply chain trust, prevent over or under supply, and stabilise the bullwhip.
Using Demand Planning Software and analytics that utilise best fit algorithms that look at demand seasonality and underlying trends can help pre-empt fluctuations in demand and enable organisations to prepare the supply chain accordingly.
Identify Where Risk Resides Within the Supply Chain
Large manufacturing organisations can rely on an array of domestic and international supply chains. Their buys may constitute a significant influence on the suppliers’ business or be a small proportion of sales. As disruptions occur, suppliers may prioritise where they can fulfil demand and where they cannot. In times of crisis, the suppliers’ capacity may even be seconded by governments.
By surveying and comprehensively understanding the supply chain, areas of risk can be identified, and contingency plans developed to mitigate the impacts of where failures can occur. This supply chain assessment may be required at multiple levels upstream within the supply chain. Tools such as Failure Modes Effects Analysis (FMEA) can be utilised to map out potential risk areas within the supply chain and attribute severity and risk factors to each mode. This can also provide a foundation to prepare Contingency Plans for the highest risk areas.
Consider TCO and Shorten the Supply Chain
Long distance global supply chains may look attractive at face value with lowest transactional cost, but volatile conditions can bring the less-obvious costs of running supply chains to the forefront.
A Total Cost of Ownership (TCO) approach enables businesses to look not only at the transaction expense, but many other factors that indirectly impact the cost of running the supply chain.
While the transactional cost of a good may be Y, when considering all the TCO elements, total costs can be Yx2 or more. If the supply chain fails, the replacement expense can be extremely costly to businesses.
Be Flexible: single-source supply chains may offer consistency and leverage but when they fail, all the eggs are in one basket. Consider dual or even multiple supply chains to distribute the risk and enhance capacity. When upstream supply partners need to deviate from standard suppliers and processes, work with them to qualify and attain flexibility as needed.
Consider Localised Solutions: while they may not be as competitive on face transactional cost, the indirect TCO factors will offset and mitigate the exposures of not being able to produce at all and the potential loss of market share. Vendor Managed Inventory (VMI) partners can offer localised supply chain partnerships leveraged with both the expertise in specialised supply chain areas and a consolidated buying power.
Shorten the Supply Chain lead times where possible to develop as much flexibility to be able to react to the disruptive dynamics impacting supply. Buy in smaller multiples or minimum order quantities in conjunction with shorter lead times. This will minimise working capital outlays and remove lumpiness from the supply chain stabilizing the bullwhip effect.
Adopting some or all of these remedies will help your organisation mitigate the effects of a volatile environment and minimise disruption.